تأثیر مواد اولیه بر کیفیت سیمان تولیدی
صنعت سیمان به عنوان یکی از پایه های اصلی صنعت ساخت و ساز نقش حیاتی در توسعه زیرساخت ها و پایداری سازه های مدرن ایفا می کند. کیفیت سیمان تولیدی نه تنها بر مقاومت و دوام بتن تأثیر مستقیم دارد بلکه بر هزینه ها زمان اجرا و حتی ملاحظات زیست محیطی نیز اثرگذار است. این کیفیت تابعی پیچیده از عوامل متعددی است که مهم ترین آن ها ماهیت و ویژگی های مواد اولیه ورودی به فرآیند تولید سیمان است. درک عمیق نحوه تأثیرگذاری این مواد از سنگ آهک و رس گرفته تا مواد افزودنی و ناخالصی ها برای تولید سیمانی با عملکرد مطلوب و مطابق با استانداردهای جهانی امری ضروری است. این مقاله به بررسی جامع این تأثیرات می پردازد و نقش حیاتی کنترل کیفیت مواد اولیه در دستیابی به محصول نهایی برتر را تبیین می کند.
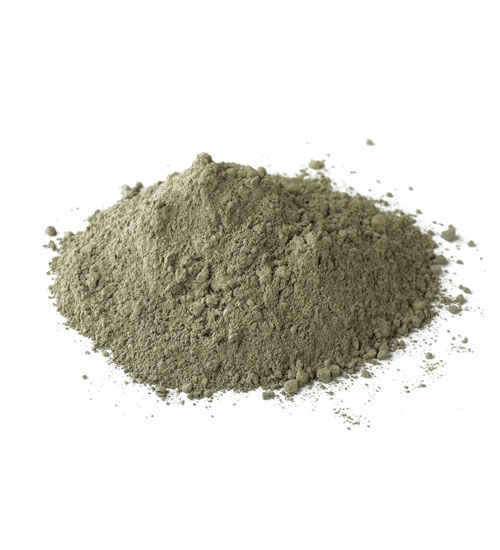
مواد اولیه با کیفیت بالا پایداری شیمیایی و فیزیکی مناسب و ترکیب دقیق امکان کنترل بهتر فرآیند پخت کلینکر و تولید فازهای معدنی مطلوب (مانند تری کلسیم سیلیکات C₃S و دی کلسیم سیلیکات C₂S) را فراهم می آورند که مستقیماً بر مقاومت اولیه و نهایی سیمان تأثیر می گذارند. از سوی دیگر وجود ناخالصی های بیش از حد یا نامطلوب می تواند منجر به مشکلاتی نظیر گیرش غیرعادی انبساط حجمی ناخواسته کاهش دوام در برابر عوامل محیطی خورنده (مانند سولفات ها) و حتی کاهش مقاومت مکانیکی شود. لذا شناسایی ارزیابی و کنترل دقیق مواد اولیه در هر مرحله از اکتشاف تا ورود به کوره ستون فقرات تولید سیمان با کیفیت و قابل اعتماد است که تضمین کننده سلامت و پایداری سازه های بتنی برای نسل های آینده خواهد بود. قیمت سیمان برگرفته از عوامل متعددی است که با توجه به این عوامل تعیین می شود و در سازمان بورس به روزرسانی می شود.
مقدمه ای بر سیمان و اهمیت کیفیت آن
سیمان ماده چسباننده ای است که در ترکیب با آب ماسه و شن بتن را تشکیل می دهد. بتن پرکاربردترین ماده ساختمانی در جهان است و کیفیت آن به شدت به کیفیت سیمان مورد استفاده بستگی دارد. سیمان پرتلند رایج ترین نوع سیمان از آسیاب کردن کلینکر (محصول پخت مخلوطی از سنگ آهک و مواد رسی در دمای بالا) به همراه مقداری گچ تولید می شود.
کیفیت سیمان اهمیت فوق العاده ای در صنعت ساختمان دارد. سازه های بتنی از پل ها و آسمان خراش ها گرفته تا خانه های مسکونی باید دارای مقاومت دوام و پایداری کافی باشند تا در برابر بارهای وارده عوامل محیطی نظیر رطوبت یخ زدگی مواد شیمیایی خورنده و زمین لرزه مقاومت کنند. استفاده از سیمان با کیفیت پایین می تواند منجر به کاهش مقاومت بتن ترک خوردگی پوسته شدن و در نهایت تخریب زودرس سازه شود که پیامدهای اقتصادی و جانی جبران ناپذیری در پی دارد. بنابراین تضمین کیفیت سیمان در تمام مراحل تولید از انتخاب مواد اولیه تا محصول نهایی امری حیاتی است.
مواد اولیه نقش اساسی و تعیین کننده ای در کیفیت نهایی سیمان ایفا می کنند. ترکیب شیمیایی و کانی شناسی مواد اولیه نسبت های اختلاط آن ها و میزان ناخالصی های موجود مستقیماً بر فرآیند پخت کلینکر تشکیل فازهای مطلوب در کلینکر و در نهایت بر خواص هیدراسیون مقاومت دوام و سلامت سیمان تولیدی تأثیر می گذارد.
مواد اولیه اصلی در تولید سیمان
تولید سیمان پرتلند عمدتاً بر پایه چهار اکسید اصلی استوار است: اکسید کلسیم (CaO) اکسید سیلیسیم (SiO₂) اکسید آلومینیم (Al₂O₃) و اکسید آهن (Fe₂O₃). این اکسیدها از مواد اولیه طبیعی مانند سنگ آهک و رس تأمین می شوند. علاوه بر این دو ماده اصلی مقادیر کمتری از سایر مواد نیز ممکن است مورد نیاز باشد.
سنگ آهک: نقش و اهمیت آن در ترکیب سیمان
سنگ آهک (Limestone) با فرمول شیمیایی اصلی کربنات کلسیم (CaCO₃) اصلی ترین ماده اولیه در تولید سیمان است و حدود 80-75 درصد مخلوط خام را تشکیل می دهد. سنگ آهک منبع اصلی اکسید کلسیم (CaO) در کلینکر سیمان است. در کوره سیمان کربنات کلسیم در دمای حدود 900 درجه سانتی گراد تجزیه شده و آهک زنده (CaO) و دی اکسید کربن (CO₂) تولید می کند (فرآیند کلسیناسیون).
کیفیت سنگ آهک از نظر میزان خلوص و درصد CaCO₃ اهمیت حیاتی دارد. سنگ آهک با خلوص بالا (بیش از 90% CaCO₃) برای تولید سیمان مطلوب است. وجود ناخالصی هایی مانند اکسید منیزیم (MgO) سیلیس آزاد (SiO₂) آلومینا (Al₂O₃) و اکسید آهن (Fe₂O₃) در سنگ آهک می تواند بر ترکیب شیمیایی کلینکر و در نتیجه بر خواص سیمان تأثیر بگذارد. به عنوان مثال MgO بیش از حد می تواند باعث انبساط حجمی ناخواسته در سیمان سخت شده شود (سلامت سیمان را به خطر می اندازد). همچنین ناخالصی ها بر دمای پخت و مصرف انرژی در کوره نیز اثرگذارند.
نحوه آماده سازی سنگ آهک شامل مراحل استخراج (معمولاً از معادن روباز) خردایش اولیه و ثانویه برای رسیدن به اندازه مناسب و سپس ذخیره سازی و پیش همگن سازی (Pre-homogenization) برای کاهش تغییرات در ترکیب شیمیایی ورودی به کارخانه است.
رس: تأثیر رس بر خواص هیدرولیکی سیمان
رس (Clay) دومین ماده اولیه اصلی در تولید سیمان است و حدود 20-15 درصد مخلوط خام را تشکیل می دهد. رس منبع اصلی اکسیدهای سیلیسیم (SiO₂) آلومینیم (Al₂O₃) و اکسید آهن (Fe₂O₃) است که همراه با CaO حاصل از سنگ آهک فازهای اصلی کلینکر سیمان را در دمای بالا تشکیل می دهند. انواع رس ها شامل کائولینیت ایلیت و مونتموریلونیت هستند که ترکیب کانی شناسی آن ها بر واکنش پذیری در کوره تأثیر می گذارد.
رس ها به دلیل ساختار لایه ای و وجود هیدروکسیل ها در دمای پایین تر از سنگ آهک تجزیه می شوند و اکسیدهای فعال خود را آزاد می کنند. نسبت رس به سنگ آهک در مخلوط خام تعیین کننده نسبت اکسیدهای اصلی و در نتیجه نسبت فازهای کلینکر (C₃S, C₂S, C₃A, C₄AF) است. این نسبت ها مستقیماً بر خواص هیدرولیکی سیمان از جمله سرعت گیرش مقاومت اولیه و نهایی و مقاومت در برابر عوامل خورنده (مانند سولفات ها) تأثیر می گذارند.
خلوص رس نیز اهمیت دارد. وجود ناخالصی هایی مانند سولفات ها می تواند زمان گیرش را تحت تأثیر قرار دهد یا باعث انبساط حجمی در سیمان سخت شده شود. مواد آلی نیز می توانند در فرآیند پخت مشکل ایجاد کنند. آماده سازی رس نیز شامل خردایش و در صورت نیاز خشک کردن و پیش همگن سازی است.
سایر مواد افزودنی: نقش و اهمیت آنها در بهبود خواص سیمان
علاوه بر سنگ آهک و رس مواد دیگری نیز ممکن است به مخلوط خام یا به کلینکر آسیاب شده اضافه شوند تا ترکیب شیمیایی را تنظیم کرده یا خواص سیمان را بهبود بخشند. این مواد افزودنی را می توان به دو دسته اصلی تقسیم کرد: مواد افزودنی اصلی (مانند پوزولان ها و سرباره) که بخشی از سیمان نهایی می شوند و مواد افزودنی فرعی (مانند گچ) که برای کنترل خواص خاص اضافه می شوند.
برخی از مهم ترین مواد افزودنی عبارتند از:
- پوزولان ها (Pozzolans): موادی حاوی سیلیس و آلومینا به شکل فعال که خودشان خاصیت چسبانندگی ندارند یا کم دارند اما در حضور رطوبت و هیدروکسید کلسیم (Ca(OH)₂) که محصول هیدراسیون سیمان است واکنش می دهند و ترکیبات چسباننده (C-S-H) تولید می کنند. پوزولان ها مقاومت نهایی دوام و مقاومت در برابر سولفات ها را افزایش داده و حرارت هیدراسیون را کاهش می دهند. نمونه ها شامل خاکستر بادی (Fly Ash) میکروسیلیس (Silica Fume) و پوزولان های طبیعی (مانند خاکستر آتشفشانی) هستند.
- سرباره کوره بلند (Blast Furnace Slag): محصول جانبی صنعت فولاد که حاوی اکسیدهای مشابه کلینکر سیمان است و خاصیت هیدرولیکی پنهان دارد. سرباره آسیاب شده (GGBS) می تواند جایگزین بخشی از کلینکر شود و مقاومت در برابر سولفات ها دوام و مقاومت نهایی را بهبود بخشد.
- خاکستر بادی (Fly Ash): محصول جانبی احتراق زغال سنگ در نیروگاه های حرارتی. حاوی سیلیس و آلومینا فعال است و به عنوان پوزولان عمل می کند. استفاده از خاکستر بادی باعث کاهش حرارت هیدراسیون بهبود کارایی بتن تازه و افزایش دوام می شود.
استفاده از این مواد افزودنی نه تنها باعث بهبود خواص عملکردی سیمان می شود بلکه می تواند به کاهش مصرف کلینکر (و در نتیجه کاهش انتشار CO₂ و مصرف انرژی) و استفاده مجدد از ضایعات صنعتی کمک کند.
تأثیر نسبت مواد اولیه بر خواص سیمان
نسبت دقیق مواد اولیه در مخلوط خام عامل کلیدی در تعیین ترکیب شیمیایی کلینکر و در نتیجه خواص سیمان نهایی است. شیمیدانان سیمان از پارامترهایی به نام مدول های شیمیایی برای کنترل این نسبت ها استفاده می کنند. مهم ترین این مدول ها عبارتند از:
- ضریب اشباع آهکی (Lime Saturation Factor – LSF): نشان دهنده نسبت CaO به سایر اکسیدها در مخلوط خام است. LSF بر میزان تشکیل فازهای C₃S و CaO آزاد در کلینکر تأثیر می گذارد. LSF بالاتر منجر به تشکیل بیشتر C₃S (مسئول مقاومت اولیه) و در صورت بالا بودن بیش از حد CaO آزاد (باعث انبساط) می شود.
- مدول سیلیسی (Silica Modulus – SM): نسبت SiO₂ به مجموع Al₂O₃ و Fe₂O₃. SM بر میزان فازهای سیلیکاتی (C₃S و C₂S) و فازهای مذاب (C₃A و C₄AF) در کلینکر تأثیر می گذارد. SM بالاتر یعنی سیلیس بیشتر و فازهای سیلیکاتی بیشتر که منجر به مقاومت بالاتر می شود اما دمای پخت را افزایش می دهد.
- مدول آلومینی (Alumina Modulus – AM): نسبت Al₂O₃ به Fe₂O₃. AM بر نسبت فازهای C₃A و C₄AF در کلینکر تأثیر می گذارد. AM بالاتر یعنی آلومینا بیشتر نسبت به آهن که منجر به تشکیل بیشتر C₃A (مسئول گیرش اولیه و حرارت هیدراسیون) می شود.
تنظیم دقیق این نسبت ها برای دستیابی به ترکیب فازی مطلوب در کلینکر و تولید سیمانی با خواص مورد نظر (مانند مقاومت فشاری زمان گیرش و دوام) حیاتی است.
تأثیر نسبت سنگ آهک به رس بر مقاومت فشاری سیمان
نسبت سنگ آهک به رس مستقیماً بر ضریب اشباع آهکی (LSF) تأثیر می گذارد. افزایش نسبت سنگ آهک (در محدوده مناسب) باعث افزایش LSF و در نتیجه افزایش درصد فاز C₃S در کلینکر می شود. فاز C₃S یا تری کلسیم سیلیکات مسئول اصلی کسب مقاومت در روزهای اولیه هیدراسیون سیمان است. بنابراین افزایش نسبت سنگ آهک (تا حدی که منجر به آهک آزاد بیش از حد نشود) معمولاً باعث افزایش مقاومت فشاری اولیه و نهایی سیمان می شود.
با این حال اگر نسبت سنگ آهک بیش از حد بالا باشد تمام CaO نمی تواند با سایر اکسیدها ترکیب شده و فازهای کلینکر را تشکیل دهد که منجر به وجود آهک آزاد (Free Lime) در کلینکر می شود. آهک آزاد در مجاورت رطوبت هیدراته شده و منبسط می شود که باعث انبساط حجمی و کاهش سلامت سیمان سخت شده می گردد. از سوی دیگر کاهش بیش از حد نسبت سنگ آهک باعث کاهش LSF و درصد C₃S شده و مقاومت سیمان را کاهش می دهد.
تأثیر نسبت مواد افزودنی بر مقاومت خمشی و کششی سیمان
مواد افزودنی مانند پوزولان ها و سرباره عمدتاً از طریق واکنش پوزولانی یا هیدرولیکی پنهان در طول زمان به کسب مقاومت بتن کمک می کنند. استفاده از این مواد می تواند بر مقاومت های مختلف سیمان و بتن تأثیر بگذارد.
استفاده از پوزولان ها و سرباره با بهبود ریزساختار خمیر سیمان سخت شده کاهش تخلخل و بهبود ناحیه انتقال بین خمیر سیمان و سنگدانه ها می تواند منجر به افزایش مقاومت خمشی و کششی بتن شود که برای کاربردهای سازه ای خاص حائز اهمیت است. برای تماشای ویدئوهای مربوط به روند تولید و کیفیت سیمان به آپارات الومتریال مراجعه نمایید.
تأثیر نسبت مواد اولیه بر زمان گیرش سیمان
زمان گیرش سیمان (Setting Time) مدت زمانی است که سیمان پس از اختلاط با آب سفتی اولیه خود را از دست داده و شروع به سخت شدن می کند. زمان گیرش مناسب برای حمل ریختن و پرداخت بتن ضروری است.
شرح عوامل موثر بر زمان گیرش سیمان:
- ترکیب فازی کلینکر: فاز C₃A (تری کلسیم آلومینات) در کلینکر با سرعت بسیار بالایی با آب واکنش می دهد و باعث گیرش آنی می شود. فاز C₃S نیز به سرعت واکنش می دهد و در گیرش اولیه نقش دارد.
- مقدار و نوع گچ: گچ (سولفات کلسیم) در مرحله آسیاب کلینکر اضافه می شود. گچ با فاز C₃A واکنش داده و لایه ای از اترینگایت (Ettringite) در اطراف ذرات C₃A تشکیل می دهد که از واکنش سریع C₃A جلوگیری کرده و زمان گیرش را تنظیم می کند. مقدار بهینه گچ برای هر کلینکر متفاوت است.
- ریزی سیمان: سیمان ریزتر سطح تماس بیشتری با آب دارد و سریع تر هیدراته می شود که منجر به گیرش سریع تر می گردد.
- دما: دمای بالاتر باعث تسریع واکنش های هیدراسیون و کاهش زمان گیرش می شود.
- مواد افزودنی: برخی مواد افزودنی شیمیایی (مانند روان کننده ها و دیرگیرکننده ها) می توانند زمان گیرش را تغییر دهند. همچنین برخی ناخالصی ها در مواد اولیه (مانند سولفات های محلول در رس) می توانند زمان گیرش را تحت تأثیر قرار دهند.
روش های تنظیم زمان گیرش سیمان:
- تنظیم دقیق مقدار گچ اضافه شده به کلینکر در مرحله آسیاب.
- کنترل ترکیب شیمیایی مخلوط خام برای تنظیم درصد فاز C₃A در کلینکر.
- کنترل ریزی سیمان در آسیاب نهایی.
- استفاده از مواد افزودنی شیمیایی تنظیم کننده زمان گیرش در بتن.
تأثیر ناخالصی های موجود در مواد اولیه بر کیفیت سیمان
وجود ناخالصی ها در مواد اولیه حتی در مقادیر کم می تواند تأثیرات منفی قابل توجهی بر فرآیند تولید و کیفیت سیمان نهایی داشته باشد. کنترل و محدود کردن این ناخالصی ها امری ضروری است.
تأثیر وجود مواد آلی در سنگ آهک
مواد آلی موجود در سنگ آهک یا رس می توانند در دمای کوره بسوزند. اگر مقدار آن ها زیاد باشد می توانند باعث ایجاد مشکلاتی نظیر تغییر در شرایط احتراق تشکیل گازهای ناخواسته و تأثیر بر تشکیل فازهای کلینکر شوند. همچنین برخی مواد آلی می توانند بر فرآیند آسیاب کردن و خواص سیمان تازه (مانند هوای محبوس) تأثیر بگذارند.
تأثیر وجود سولفات ها در رس
وجود سولفات های محلول در رس (مانند گچ یا سولفات سدیم/پتاسیم) می تواند در طول فرآیند پخت تبخیر شده و در بخش های سردتر کوره یا پیش گرمکن رسوب کند و باعث گرفتگی (build-up) شود که عملکرد کوره را مختل می کند. علاوه بر این سولفات های موجود در مواد اولیه می توانند بر مقدار سولفات در کلینکر تأثیر گذاشته و در صورتی که میزان کل سولفات در سیمان نهایی از حد مجاز استاندارد تجاوز کند منجر به انبساط حجمی و کاهش سلامت سیمان سخت شده شود (به ویژه در حضور آهک آزاد یا MgO).
تأثیر وجود قلیایی ها در مواد اولیه
قلیایی ها (Alkalies) عمدتاً شامل اکسید سدیم (Na₂O) و اکسید پتاسیم (K₂O) هستند که می توانند در سنگ آهک رس و سایر مواد اولیه وجود داشته باشند. قلیایی ها در دمای کوره تبخیر شده و در بخش های سردتر رسوب می کنند که می تواند باعث گرفتگی و افزایش میزان گرد و غبار خروجی شود. مهم تر اینکه قلیایی های موجود در سیمان می توانند با برخی انواع سنگدانه های واکنش پذیر در بتن وارد واکنش شوند (واکنش قلیایی سنگدانه – Alkali-Aggregate Reaction) که منجر به انبساط ترک خوردگی و تخریب بتن در طول زمان می شود. استانداردهای سیمان حد مجاز قلیایی ها را برای کنترل این پدیده مشخص می کنند.
سایر ناخالصی ها مانند اکسید منیزیم (MgO) فسفر (P₂O₅) و کلریدها (Cl⁻) نیز می توانند تأثیرات منفی داشته باشند. MgO بیش از حد (به ویژه در سنگ آهک) باعث انبساط پری کلاز (Periclase – MgO بلوری) و کاهش سلامت سیمان می شود. P₂O₅ می تواند بر تشکیل فاز C₃S تأثیر منفی گذاشته و مقاومت سیمان را کاهش دهد. کلریدها (به ویژه در مواد افزودنی مانند سرباره دریایی) می توانند باعث خوردگی آرماتور در بتن مسلح شوند.
فرآیند کنترل کیفیت مواد اولیه در کارخانه سیمان
کنترل کیفیت مواد اولیه یک فرآیند چند مرحله ای و حیاتی در کارخانه سیمان است که از زمان ورود مواد به کارخانه آغاز شده و تا قبل از ورود به کوره ادامه می یابد. هدف اصلی اطمینان از همگن بودن و داشتن ترکیب شیمیایی و فیزیکی مطلوب مواد ورودی به فرآیند پخت است.
نمونه برداری و آزمایش مواد اولیه
اولین گام نمونه برداری منظم و نماینده از هر بچ ورودی مواد اولیه (مانند سنگ آهک رس سنگ آهن و …) است. نمونه برداری باید بر اساس استانداردهای مشخص و به گونه ای انجام شود که معرف کل محموله باشد. نمونه های گرفته شده به آزمایشگاه کارخانه منتقل می شوند.
در آزمایشگاه آزمایش های مختلفی بر روی مواد اولیه انجام می شود:
- آزمایش های شیمیایی: تعیین درصد اکسیدهای اصلی (CaO, SiO₂, Al₂O₃, Fe₂O₃) و ناخالصی ها (MgO, SO₃, Na₂O, K₂O, Cl⁻, P₂O₅) با استفاده از روش هایی مانند فلورسانس پرتو ایکس (XRF) یا روش های شیمی تر. این آزمایش ها برای محاسبه مدول های شیمیایی و کنترل ترکیب مخلوط خام ضروری هستند.
- آزمایش های فیزیکی: تعیین رطوبت دانه بندی چگالی و در برخی موارد مقاومت فشاری یا ویژگی های حرارتی.
- آزمایش های کانی شناسی: استفاده از روش هایی مانند پراش پرتو ایکس (XRD) برای شناسایی فازهای کانیایی موجود در مواد اولیه که بر واکنش پذیری آن ها در کوره تأثیر می گذارد.
تطبیق مواد اولیه با استانداردهای ملی و بین المللی
نتایج آزمایش های انجام شده بر روی مواد اولیه با الزامات استانداردهای مربوطه مقایسه می شوند. هرچند استانداردهای سیمان عمدتاً خواص محصول نهایی (سیمان) را مشخص می کنند اما برخی استانداردها یا دستورالعمل های داخلی کارخانه نیز ممکن است برای مواد اولیه ورودی حدود قابل قبول برای ترکیب شیمیایی و ناخالصی ها را تعیین کنند. این امر به اطمینان از مناسب بودن مواد اولیه برای تولید سیمان مطابق با استاندارد محصول نهایی کمک می کند.
اصلاح و بهینه سازی ترکیب مواد اولیه بر اساس نتایج آزمایش ها
بر اساس نتایج آزمایش های شیمیایی ترکیب مخلوط خام (نسبت سنگ آهک رس و سایر مواد کمکی مانند سنگ آهن یا بوکسیت) تنظیم می شود تا مدول های شیمیایی (LSF, SM, AM) در محدوده هدف برای تولید کلینکر مورد نظر قرار گیرند. این تنظیمات به صورت پیوسته و بر اساس آنالیزهای نمونه های مخلوط خام قبل از ورود به آسیاب مواد خام یا سیلوهای همگن سازی انجام می شود. استفاده از سیستم های کنترل کیفیت آنلاین (مانند آنالایزرهای XRF مسیر) می تواند به تنظیم خودکار و بلادرنگ ترکیب مخلوط خام کمک کند.
فرآیند پیش همگن سازی (Pre-homogenization) در دپوهای مواد اولیه با انباشت لایه ای و برداشت عمودی مواد به کاهش تغییرات در ترکیب شیمیایی ورودی به کارخانه و سهولت تنظیم مخلوط خام کمک شایانی می کند.
استانداردهای مربوط به مواد اولیه سیمان
در حالی که اکثر استانداردهای سیمان بر خواص محصول نهایی تمرکز دارند اما کیفیت مواد اولیه به طور غیرمستقیم توسط این استانداردها کنترل می شود زیرا مواد اولیه باید امکان تولید سیمانی را فراهم کنند که الزامات استانداردها را برآورده سازد. با این حال برخی استانداردها ممکن است به طور مستقیم یا غیرمستقیم به مواد اولیه یا مواد افزودنی مورد استفاده در تولید سیمان اشاره کنند.
معرفی استانداردهای ملی ایران (ISIRI)
سازمان ملی استاندارد ایران (ISIRI) استانداردهای مختلفی را برای انواع سیمان و مواد مرتبط تدوین کرده است. استاندارد اصلی سیمان پرتلند استاندارد ISIRI 389 است که انواع مختلف سیمان پرتلند را بر اساس ترکیب خواص فیزیکی و مکانیکی و شیمیایی طبقه بندی و الزامات آن ها را مشخص می کند. این استاندارد محدودیت هایی را برای ترکیب شیمیایی سیمان نهایی (مانند درصد SO₃ MgO قلیایی ها افت حرارتی و باقیمانده نامحلول) تعیین می کند که این محدودیت ها مستقیماً بر کیفیت مواد اولیه مورد نیاز برای تولید سیمان تأثیر می گذارند.
علاوه بر ISIRI 389 استانداردهای دیگری نیز برای مواد افزودنی مورد استفاده در سیمان یا بتن وجود دارند مانند استانداردهای مربوط به خاکستر بادی سرباره کوره بلند و پوزولان های طبیعی که ترکیب شیمیایی و خواص این مواد را مشخص می کنند. کیفیت و استاندارد بودن سیمان تاثیر بر روند قیمت سیمان و کیفیت سیمان دارد.
معرفی استانداردهای بین المللی (ASTM, EN)
استانداردهای بین المللی مانند ASTM (American Society for Testing and Materials) و EN (European Standards) نیز نقش مهمی در صنعت سیمان دارند. استاندارد ASTM C150 مشخصات سیمان پرتلند را ارائه می دهد که مشابه ISIRI 389 شامل الزامات شیمیایی و فیزیکی است.
استانداردهای اروپایی سری EN 197 انواع مختلف سیمان را بر اساس ترکیب (درصد کلینکر سرباره پوزولان خاکستر بادی و …) طبقه بندی می کنند و الزامات مربوط به هر نوع را مشخص می نمایند. این استانداردها به طور مستقیم به مواد تشکیل دهنده سیمان اشاره دارند و کیفیت و ترکیب این مواد افزودنی را نیز تحت پوشش قرار می دهند.
مقایسه استانداردهای مختلف و الزامات آنها برای مواد اولیه
اگرچه جزئیات و طبقه بندی ها در استانداردهای مختلف ممکن است متفاوت باشد اما هدف اصلی همه آن ها تضمین کیفیت و عملکرد مطلوب سیمان است. استانداردهای محصول نهایی (مانند ISIRI 389 یا ASTM C150) با تعیین محدودیت برای ناخالصی های مضر در سیمان نهایی (نظیر MgO SO₃ قلیایی ها) عملاً کیفیت مواد اولیه را کنترل می کنند. استانداردهایی که به مواد افزودنی (مانند EN 197 یا استانداردهای جداگانه برای پوزولان ها و سرباره) می پردازند ترکیب شیمیایی فعالیت پوزولانی یا هیدرولیکی و سایر ویژگی های این مواد را مشخص می کنند تا اطمینان حاصل شود که استفاده از آن ها در سیمان خواص مطلوب را ایجاد کرده و اثرات نامطلوب نداشته باشد.
روش های بهبود کیفیت مواد اولیه سیمان
حتی با انتخاب دقیق منابع مواد اولیه استخراج شده ممکن است نیاز به پردازش و بهبود داشته باشند تا برای تولید سیمان با کیفیت مناسب شوند. روش های مختلفی برای بهبود کیفیت مواد اولیه قبل از ورود به فرآیند پخت وجود دارد.
روش های خردایش و آسیاب کردن مواد اولیه
اندازه ذرات مواد اولیه قبل از ورود به کوره اهمیت زیادی دارد. خردایش و آسیاب کردن مناسب باعث افزایش سطح تماس مواد و بهبود فرآیند کلسیناسیون و تشکیل فازهای کلینکر در کوره می شود. سنگ آهک و رس پس از خردایش اولیه و ثانویه در آسیاب مواد خام (به صورت تر یا خشک) آسیاب می شوند تا به نرمی و توزیع اندازه ای مناسب برای مخلوط خام دست یابند. کنترل دقیق فرآیند آسیاب برای دستیابی به نرمی مطلوب و اجتناب از آسیاب بیش از حد یا کمتر از حد ضروری است.
روش های حذف ناخالصی ها از مواد اولیه
برخی ناخالصی ها را می توان تا حدی از مواد اولیه حذف کرد. به عنوان مثال شستشوی رس می تواند مواد آلی محلول یا نمک ها را کاهش دهد. در برخی موارد برای حذف سیلیس آزاد یا سایر کانی های نامطلوب از سنگ آهک ممکن است از روش های کانی آرایی (Beneficiation) نظیر فلوتاسیون استفاده شود اگرچه این روش ها معمولاً پرهزینه هستند و کمتر در صنعت سیمان رایج اند. انتخاب دقیق محل استخراج در معدن نیز خود نوعی روش کنترل ناخالصی در منبع است.
روش های مخلوط کردن و همگن سازی مواد اولیه
همگن سازی (Homogenization) مواد اولیه قبل از ورود به کوره یکی از مهم ترین عوامل در کنترل کیفیت است. هدف کاهش تغییرات در ترکیب شیمیایی مخلوط خام ورودی به کوره است. این کار به روش های مختلفی انجام می شود:
- پیش همگن سازی در دپوها (Stockpile Pre-homogenization): مواد اولیه به صورت لایه ای انباشت شده و سپس به صورت عمودی برداشت می شوند تا مخلوطی از لایه های مختلف ایجاد شود.
- همگن سازی در سیلوها (Silo Homogenization): مخلوط خام آسیاب شده در سیلوهای مخصوصی که دارای سیستم هوادهی یا مکانیکی برای مخلوط کردن پودر هستند همگن می شود. این روش دقت بیشتری در همگن سازی فراهم می کند و تغییرات ترکیب شیمیایی ورودی به کوره را به حداقل می رساند که منجر به پخت پایدارتر و تولید کلینکر با کیفیت یکنواخت تر می شود.
نقش آزمایشگاه در تعیین کیفیت مواد اولیه و سیمان تولیدی
آزمایشگاه کنترل کیفیت قلب تپنده هر کارخانه سیمان است. نقش آزمایشگاه تنها به آزمایش مواد اولیه محدود نمی شود بلکه تمام مراحل فرآیند تولید را پوشش می دهد. آزمایشگاه مسئول نمونه برداری و آنالیز مواد اولیه ورودی کنترل ترکیب شیمیایی مخلوط خام آنالیز خوراک کوره کلینکر و محصول نهایی (سیمان) است.
کارشناسان آزمایشگاه با استفاده از تجهیزات پیشرفته آنالیز شیمیایی (مانند XRF) و فیزیکی ترکیب شیمیایی و خواص مواد را بررسی کرده و نتایج را به بخش تولید گزارش می دهند تا تنظیمات لازم در فرآیند انجام شود. همچنین آزمایشگاه مسئول انجام آزمایش های استاندارد بر روی سیمان تولیدی (نظیر مقاومت فشاری زمان گیرش نرمی سلامت و آنالیز شیمیایی نهایی) است تا اطمینان حاصل شود محصول نهایی با الزامات استانداردها مطابقت دارد. نقش آزمایشگاه در تضمین کیفیت پایدار و ردیابی مشکلات احتمالی در فرآیند تولید حیاتی است.
آزمایشگاه همچنین در تحقیق و توسعه برای بهبود کیفیت محصول استفاده از مواد اولیه جدید یا جایگزین و بهینه سازی فرآیند نقش دارد. دقت سرعت و قابلیت اطمینان آزمایشگاه مستقیماً بر توانایی کارخانه در تولید سیمانی با کیفیت بالا و به صورت پایدار تأثیر می گذارد.
منابع و مراجع
در نگارش این محتوا از دانش تخصصی در حوزه شیمی و تکنولوژی سیمان و استانداردهای مرتبط بهره گرفته شده است. برای اطلاعات بیشتر و جزئیات فنی دقیق تر می توان به منابع دانشگاهی و صنعتی معتبر در زمینه تکنولوژی سیمان استانداردهای ملی و بین المللی سیمان (ISIRI, ASTM, EN) و نشریات تخصصی صنعت سیمان مراجعه کرد.
چگونه می توان کیفیت سنگ آهک را برای تولید سیمان بهینه کرد؟
کیفیت سنگ آهک با انتخاب معادن با خلوص بالا کنترل دقیق در استخراج برای کاهش ناخالصی ها خردایش و آسیاب مناسب و اجرای فرآیندهای پیش همگن سازی در دپوها بهینه می شود.
چه مقدار رس باید به سنگ آهک اضافه شود تا بهترین سیمان تولید شود؟
مقدار رس به ترکیب شیمیایی رس و سنگ آهک بستگی دارد و با هدف دستیابی به مدول های شیمیایی (LSF, SM, AM) در محدوده هدف برای تولید نوع خاصی از سیمان محاسبه می شود. این نسبت با آنالیزهای شیمیایی مخلوط خام تنظیم می شود.
آیا استفاده از مواد افزودنی در تولید سیمان ضروری است؟
استفاده از گچ برای تنظیم زمان گیرش ضروری است. استفاده از سایر مواد افزودنی (پوزولان ها سرباره) برای تولید سیمان های خاص با خواص بهبود یافته (مانند مقاومت بالا دوام بیشتر حرارت هیدراسیون کمتر) یا برای کاهش هزینه و اثرات زیست محیطی (کاهش کلینکر) رایج و توصیه می شود.
چگونه می توان ناخالصی های موجود در مواد اولیه سیمان را تشخیص داد؟
ناخالصی ها از طریق آنالیزهای شیمیایی در آزمایشگاه (مانند XRF) و بررسی کانی شناسی مواد اولیه (مانند XRD) تشخیص داده می شوند. کنترل دقیق در مرحله اکتشاف و استخراج نیز به شناسایی منابع ناخالصی کمک می کند.
چه استانداردهایی برای مواد اولیه سیمان وجود دارد؟
استانداردهایی مانند ISIRI 389 ASTM C150 و EN 197 به طور غیرمستقیم با تعیین الزامات برای سیمان نهایی کیفیت مواد اولیه را کنترل می کنند. استانداردهای جداگانه نیز برای مواد افزودنی مانند خاکستر بادی سرباره و پوزولان ها وجود دارند که ترکیب و خواص آن ها را مشخص می کنند.
چگونه می توان زمان گیرش سیمان را کنترل کرد؟
زمان گیرش سیمان با تنظیم دقیق مقدار گچ اضافه شده به کلینکر کنترل ترکیب فازی کلینکر (به ویژه C₃A) کنترل ریزی سیمان و در صورت نیاز استفاده از مواد افزودنی شیمیایی در بتن کنترل می شود.
چه عواملی باعث کاهش مقاومت سیمان می شوند؟
عواملی مانند نسبت نامناسب مواد اولیه (LSF پایین) وجود ناخالصی های مضر (مانند P₂O₅) پخت نامناسب کلینکر آسیاب نامناسب سیمان (نرمی کم) و وجود ناخالصی در گچ می توانند باعث کاهش مقاومت سیمان شوند.
چگونه می توان مقاومت سیمان را افزایش داد؟
مقاومت سیمان با تنظیم بهینه نسبت مواد اولیه برای افزایش فاز C₃S در کلینکر پخت مناسب کلینکر آسیاب دقیق سیمان (افزایش نرمی در حد استاندارد) و استفاده از مواد افزودنی فعال (مانند میکروسیلیس یا سرباره) افزایش می یابد.
آیا استفاده از سیمان با کیفیت پایین در ساخت و ساز خطراتی دارد؟
بله استفاده از سیمان با کیفیت پایین خطرات جدی دارد از جمله کاهش مقاومت و دوام بتن ترک خوردگی پوسته شدن نفوذپذیری بالا و در نهایت تخریب زودرس سازه که می تواند منجر به خسارات مالی و جانی شود.
هزینه تولید سیمان با کیفیت بالا چقدر است؟
تولید سیمان با کیفیت بالا ممکن است به دلیل نیاز به مواد اولیه با خلوص بالاتر فرآیندهای کنترل کیفیت دقیق تر استفاده از تکنولوژی پیشرفته تر در پخت و آسیاب و استفاده از مواد افزودنی خاص هزینه بیشتری نسبت به سیمان معمولی داشته باشد.
آیا شما به دنبال کسب اطلاعات بیشتر در مورد "تأثیر مواد اولیه بر کیفیت سیمان تولیدی" هستید؟ با کلیک بر روی اقتصادی, کسب و کار ایرانی، ممکن است در این موضوع، مطالب مرتبط دیگری هم وجود داشته باشد. برای کشف آن ها، به دنبال دسته بندی های مرتبط بگردید. همچنین، ممکن است در این دسته بندی، سریال ها، فیلم ها، کتاب ها و مقالات مفیدی نیز برای شما قرار داشته باشند. بنابراین، همین حالا برای کشف دنیای جذاب و گسترده ی محتواهای مرتبط با "تأثیر مواد اولیه بر کیفیت سیمان تولیدی"، کلیک کنید.